Circular economy
Promoting Circular Economy Business
The conventional economic system based on mass production, mass consumption, and mass disposal has led to a variety of serious problems, including climate change, resource depletion, and plastic pollution. The advent of these issues has led to a call to shift beyond the conventional 3Rs of reduce, reuse, and recycle, to a circular economy that creates added value by providing services while reducing resource input and consumption, and making effective use of existing stock.
In addition to the sale of machinery and equipment returned on lease expiration, the SMFL Group focuses on the purchase and sale of general used machinery and equipment, with particular leadership in used semiconductor manufacturing equipment. In addition, we are actively promoting 3R activities, such as providing waste compliance management ASP services and entering the equipment and plant disposal general contracting business.
In April 2023, we established a Company-wide, crossfunctional Circular Economy Promotion Working Team that will work with SMFG and Sumitomo Corporation, our two shareholders, to help bring about a circular economy. We will achieve this by harnessing our knowledge and expertise in equipment as a leasing company and by collaborating with manufacturers, sales companies, and other partners.
With the April 2022 enforcement of Japan’s Act on Promotion of Resource Circulation for Plastics, we have set quantitative and qualitative targets for reduction of emissions of plastic office supplies used in our business activities and recycling of plastic-based materials used in properties at the end of their leases.
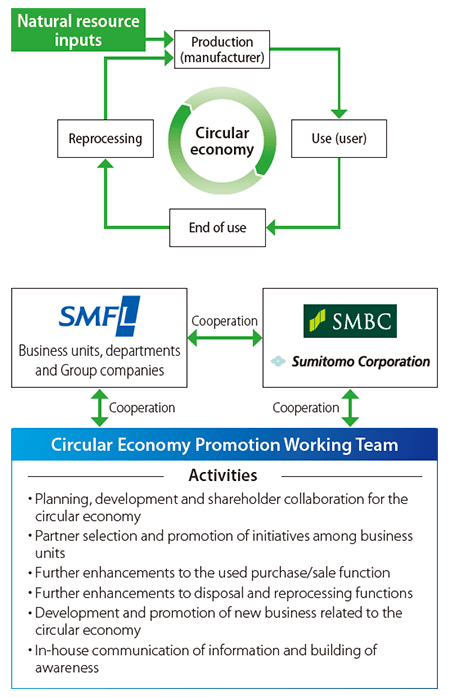
SMART: Facility and plant dismantling and disposal business

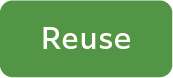
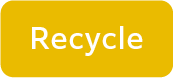
Established in 2019 as a joint venture between ARBIZ Corporation and SMFL MIRAI Partners, SMART is a general contractor for facility and plant disposal.
ARBIZ Corporation’s demolition supervision, execution, and recycling technologies, combined with the SMFL Group’s knowledge and expertise in equipment and its reuse network for used equipment, are harnessed to provide one-stop services ranging from plant demolition and equipment removal work to resale and recycling of unneeded machinery and equipment. ARBIZ handles a range of projects, not only for various facilities and plants but also piers and other structures.
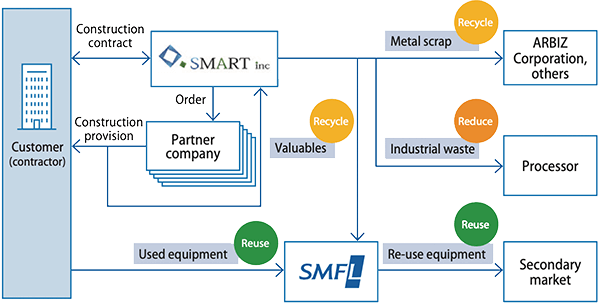
PBasis: A waste compliance management ASP service
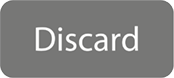
Companies aiming to realize a circular economy will find it indispensable to practice rigorous waste governance. This is a practice where emissions resulting from corporate activities are managed in an appropriate manner and in compliance with relevant laws and regulations. Our PBasis* ASP service achieves integrated management through the visualization of emissions information, from basic information on emissions, contracts, and permits, to production of manifests, and aggregation and management of waste volumes, recycling rates, and CO2 emissions. It not only bolsters compliance, but also contributes to operational efficiency and resource recycling.
- *PBasis is a registered trademark of Panasonic Holdings Corporation
Japan’s largest used machinery warehouse (Kawashima Warehouse)
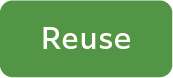
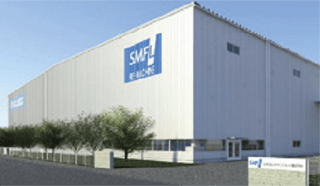
We have a used machinery storage warehouse of approximately 11,000 m², the largest in Japan. We offer a wide selection of high-demand newer used machinery and a lineup of large and small machinery. In addition, our skilled maintenance on used machinery creates a supply system for used machinery to support customers’ prompt installation of equipment.
Sale and purchase of used semiconductor manufacturing equipment
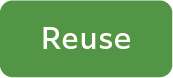
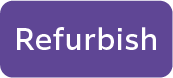
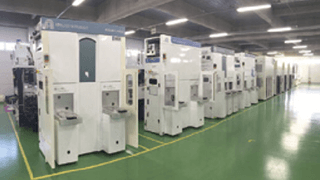
In 1994, we became the first in the industry to start a used semiconductor manufacturing equipment business. We have expanded the business worldwide and are now a world leader in volume. By leveraging the funding capability of a financial company and the ability to assess semiconductor manufacturing equipment cultivated over a number of years in the industry, we won orders in FY2021 for all three major large-scale projects where pieces of equipment were put up for sale from semiconductor production lines in Japan. We have also recently begun to offer technical services associated with used equipment sale and purchase, and our specialized engineers and partner companies respond to various needs at customers’ factories.
Collaboration with manufacturers
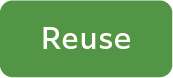
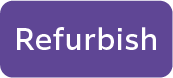
Restoring a grinding machine scheduled to be scrapped to like-new condition
We purchased a grinding machine that was scheduled to be scrapped after 30 years of use. Okamoto Machine Tool Works, Ltd. and Giken Co., Ltd. refurbished it and restored it to like-new condition.
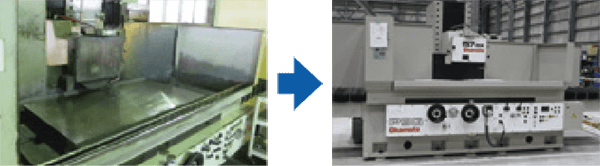
Improving the reuse rate by adding manufacturer maintenance and inspection service for used machines
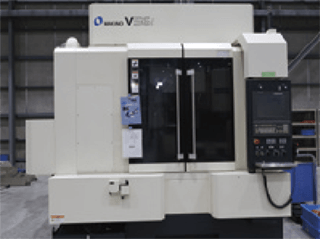
We added maintenance and inspection services by Makino Milling Machine Co., Ltd. for the used machining centers we sell, improving the reuse rate.
Contributing to corporate activities
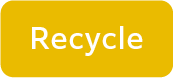

Fuel cell power generation using biogas derived from brewery wastewater
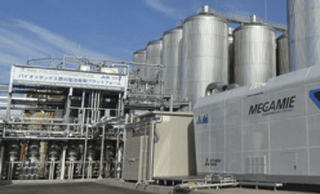
We worked with Asahi Group Holdings, Ltd. to conduct a demonstration project at Asahi Breweries’ Ibaraki Brewery of power generation from fuel cells using biogas derived from beer brewery wastewater as a new model for reducing CO2 emissions. This demonstration project was implemented under the Ministry of the Environment’s Low Carbon Technology Research, Development and Demonstration Program in Japan for subsidizing projects that contribute to reducing CO2 emissions. We provided financing for the equipment, including the fuel cell equipment provided by Mitsubishi Heavy Industries, Ltd., and coordinated the entire project as lead applicant. Operation commenced in October 2020, and the demonstration project was completed in March 2022. Full-scale operation of the equipment will make it possible to supply approximately 1.6 million kWh of electricity annually (enough to power approximately 350 typical households), which is expected to reduce CO2 emissions by approximately 1,000 tons annually. Going forward, we will continue to work with partner companies to leverage the strengths of each company and promote initiatives aimed at reducing CO2 emissions, thereby contributing to the realization of a decarbonized society.
Supporting the promotion of recycling surplus food into feed
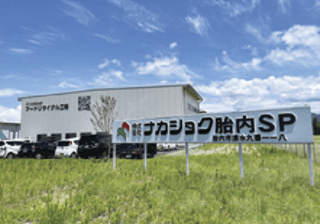
We provided financing to support the installation of refrigeration equipment for Nakasyoku Co., Ltd.’s efforts to recycle surplus sweets and food into feed. Most raw materials for feed are imported to Japan, but unusual weather and other factors have caused international prices to skyrocket, threatening the sustainable management of livestock businesses. Nakasyoku is a livestock business that produces eggs and pork in Niigata Prefecture. It uses its unique expertise to convert unconsumed food ingredients such as sweets and sake lees before expiration into feed. Through our financing support, Nakasyoku solved the problem of storing raw materials such as chocolate in the summer and expanded the range of items they process. In addition, our support in building win-win relationships is facilitating Nakasyoku’s efforts to connect with food manufacturers struggling to reduce the amount of food waste. Through these efforts, the volume of materials processed is increasing and is expected to reach 10,000 tons per year. In addition to leasing and other financing services, we are working to provide a stable supply of food and reduce food waste by providing services that go beyond the bounds of finance.